Hydraulikk og pneumatikk
/Hydraulikk og pneumatikk er svært effektive og smarte måter å overføre mekanisk kraft på. Væsker og gasser har den egenskap at de former seg til omgivelsene og sprer seg likt utover hele det området de har tilgjengelig. De er "smidige" og kan overføre kraft på rare måter og i merkverdige vinkler.
Ordet hydraulikk kommer fra latin, 'hydro' som betyr "vann" og pneumatikk kommer av ordet 'pneuma' som betyr "pust" eller "sjel".
Hydraulikk er læren om væske i bevegelse og trykk i mekaniske systemer, rettere kalt hydrodynamikk og hydrostatikk respektivt.
En fundamental egenskap med væsker er at de er så godt som ukomprimerbare. Det vil si at de er veldig egnet til å omdirigere trykk og kraft.
Dette er hovedforskjellen mellom hydraulikk og trykkluft, siden trykkluft baserer seg på gass, hvilket ER komprimerbar. Væske er teknisk sett komprimerbar, men det komprimerer seg maksimalt ca. 1,5% under enormt trykk.
Hydraulikk brukes når man trenger ren kraftoverføring. Trykkluft brukes i systemer som trenger å slå raskt ut eller være fjæret, som luftfjæring i biler.
Siden ca. 1950 har hydraulikk vært standard teknologi i konstruksjonsmaskiner og er i dag brukt overalt i tung industri, styresystemer, bremsemekanismer, etc. og spiller en stor rolle innen gruvedrift, landbruk m.m.
Pneumatikk er på mange måter likt som damp med tanke på at begge bygger på å komprimere gass, men hovedforskjellen er hvordan de oppnår trykket. Dampdrift oppnås ved å koke vann og lage vanndamp under høyt trykk, noe som skaper veldig mye energi og er hvordan de fleste atomreaktorer lager strøm. Men dampen blir til vann igjen når den avkjøles og den er varm når den er i bruk. Trykkluft er også komprimert gass, men den komprimeres med en kompressor og er kald når den kommer ut og kondenserer ikke slik at den kan brukes på mange felt der damp ville vært upraktisk.
Trykkluft er ikke like effektivt som hydraulikk når det kommer til tungt maskineri, men har mange andre bruksområder og er en svært utbredt teknologi som brukes i transport, styresystemer, fjæringssystemer, robotikk, målesystemer og mye annet. Pneumatikk er også på mange områder "raskere" enn hydraulikk pga. lavere viskositet, mer om det senere.
Pneumatiske sylindre (Pneumatic actuators)
Hydrauliske sylindre (Hydraulic actuators)
Fundamentale prinsipper innen hydraulikk
Grunnprinsippene innen hydraulikk er ofte kreditert til den franske fysikeren Blaise Pascal, og som så mange vitenskapsmenn fra den tiden har han selvsagt en lov og enhet oppkalt etter seg.
Pascal's lov sier at en trykkendring som forekommer hvor som helst i et lukket system med ukomprimerbar væske sprer seg slik at det samme trykket er likt overalt i systemet.
Grunnprinsippene er:
Væsker former seg til beholderen
Væsker er praktisk sett ukomprimerbare
Væsker sprer trykk likt i alle retninger
Væsker former seg til beholderen
Væske vil spre seg likt ut til samme nivå og ut i alle kriker og kroker som væskens trykk overkommer.
Væsker er praktisk sett ukomprimerbare
Væsker komprimerer seg ca 1-1,5% under et trykk på 20000 kPa (kiloPascal). Hydraulisk olje, hvilket er det som stort sett blir brukt i slike systemer regnes for å være så godt som ukomprimerbar, samt at den smører systemet og hindrer korrosjon.
Væskens molekyler ligger pakket slik at de ikke lar seg pakke tettere. Økt trykk på systemet øker trykket, men væskens volum forblir det samme.
Væsker sprer trykk likt i alle retninger
Trykket i et hydraulisk system er likt overalt i systemet.
I flasken til høyre, som er et ofte brukt eksempel på Pascals lov, påføres det et trykk på korken. Dette trykket er likt i hele flasken pga. væsken.
Når en sylinder er koblet til en annen lik sylinder via en slange eller rør vil en volumendring i den ene sylinderen gi en lik volumendring i den andre sylinderen. Trykket i systemet vil være likt overalt.
Væsker er praktiske for å overføre kraft gjennom slanger og rør, gjennom hjørner og andre rare vinkler og veier.
Trykk-trekanten
Trykk i hydrauliske og pneumatiske systemer måles i Pascal.
1 Pascal er 1 Newton per kvadratmeter
1 Newton er kraften som trengs for å gi 1 kilo en hastighet på 1m/s på ett sekund
1 Kilogram er lik 9.80665002864 Newton, som er tyngdekraften til jorden. Dette blir vanligvis rundet av til 9,8 Newton, eller 10 om man er grov i målet .
Trykk benevnes som oftest i kiloPascal (kPa)
Trykk beskrives også i Bar. 1 Bar er lik 1 atmosfære (atm) (nesten; det er 1.01325 Bar) og er trykket ved havnivået
1 kPa er 1/100 Bar, altså er 1 Bar = 100 kPa eller 100 000 Pascal (10⁵ ). 1 MegaPascal (MPa), 1 million Pascal = 10 Bar
Formlene er som følger:
Kraft = Trykk x Areal (F = p x A)
Trykk = Kraft / Areal (p = F / A)
Areal = Kraft / Trykk (A = F / p)
Det er litt forvirrende når vi er vant til metrisk at alle enheter er delelige på 1000 med hverandre or er direkte relaterte at 1 Bar er 100 000 Pa, men det får vi leve med.
I det imperiske system brukes PSI for å måle trykk som står for "pound-force per square inch" og jeg må ærlig talt innrømme at jeg er litt misunnelig på akkurat denne måten å benevne det på. Ja, Pascal gjør akkurat den samme jobben, mye bedre også siden den er en SI enhet, men med PSI er hele formelen oppgitt i enheten og enheten er kun et amalgam av de to variablene man behøver for å finne den;
Kraft måles i pund hvor ett pund er 4.44822 Newton
Areal måles i kvadrattommer hvor en tomme er 2,54 cm og en kvadrattomme er 0.00064516 m²
Atmosfærisk trykk og vekten av vann
I tillegg til trykket man tilfører hydrauliske og pneumatiske systemer er det som sagt et konstant trykk på alt som befinner seg på bakkenivå, kalt 1 atmosfære trykk. Luft veier ikke stort, men når man regner med all luften som befinner seg innen en søyle på 1 kvadratmeter fra bakken og opp til kanten av atmosfæren blir vekten betydelig, ca 10 tonn! Dette trykket som befinner seg på bakkenivå, og som vi alle opplever, kalles en standard atmosfære og er som sagt lik 101 325 Pa, ofte avrundet til 100 000 Pa, som er 1 Bar eller 14,7 PSI.
De fleste trykkmålere kompenserer for dette trykket og viser 0 kPa ved bakkenivå, altså standardtrykk. Trykket i et system som også tar hensyn til atmosfærisk trykk refereres til som absolutt trykk. Når trykket ved havnivået går under atmosfærisk trykk i et system kalles dette et vakuum, og absolutt vakuum vil tilsvare et absolutt trykk på 0 kPa.
Når man dykker er trykket på den dybden man dykker til ofte oppgitt i atmosfærer.
En kubikkmeter vann inneholder 1000 liter og veier da 1000 kg. 1 kubikkmeter vann utgjør en kraft nedover på 9806.650 Newton så med litt matte kan vi regne oss frem til at 1 atmosfæres trykk under vann oppstår 101 325 / 9806.650 = 10, 3 meter under vann. Så når vi befinner oss 10,3 meter under vann opplever vi 2 atmosfærer, vekten av luften pluss vekten av vannet over oss. 20,6 meter ned er da 3 atmosfærer, osv...
Så hvordan funker det i praksis?
Den fundamentale tredje egenskapen til hydraulikk og pneumatikk, at trykket sprer seg likt i alle retninger vil da si dersom man påfører et trykk i en væske vil trykket påføre størst kraft på den største overflaten. Trykket er likt overalt, men siden kraft = trykk X areal vil et større areal ha større kraftpotensiale.
Tegningen over et typisk eksempel for å forstå konseptet. En kraft F1, la oss si 50 N, trykker på stempel A1 som har en overflate eksponert til den hydrauliske væsken på 0,001 m², hvor stort trykk blir det i væsken?
Så hvis stempel A2 har et areal på 0,01 m², hva blir da kraften vi får ut i F2?
Vi ser at med en 10-dobling av arealet har vi 10-doblet kraften vi puttet inn i systemet. Dette er på mange måter det samme forholdet som gjelder for tannhjul. Et tannhjul som drives av et 10 ganger mindre tannhjul vil ha 10 ganger kraften som blir tilført det drivende hjulet, men det lille hjulet må gå 10 ganger rundt for at det store skal gå en gang rundt. Det samme gjelder hydrauliske systemer. Hvis man 10-dobler arealet får man 10 ganger kraften, men stempelet går bare 1/10 av distansen som det lille gjør. Så man må presse det lille stempelet 10 ganger så langt som den distansen man vil oppnå med det store.
Det motsatte er også sant som man kan observere på f.eks. sprøyter. Det krever en del trykk for å presse ut væsken, men den skyter ut fortere og mye lengre ut av kanylen enn det man presser på sprøyten.
En liten kraft over en lang avstand erstattes med en stor kraft over en liten avstand og vice versa.
Siden trykket i systemet er likt overalt vil et trykk på 1 Pa være 1 Newton per kvadratmeter, så når man får dette trykket til å trykke på noe som er 10 kvadratmeter vil trykket på den flaten være 10 Pa! Magi!
Så dersom jeg vil løfte en hel bil med en hydraulisk jekk, kun med min egen kroppsvekt, hvor bilen veier 1,5 tonn og jeg veier 65 kilo, hvor liten må sylinderen jeg står på være?
Vel, min kroppsvekt har en kraft på 637.432 Newton mot bilens 14709.975 N. Vi kan med en gang se at sylinderen må være (14709 / 637 = 23,1) hvertfall over 23,5 ganger mindre enn drivstempelet, som er 0,05 m², som gjør at den må bli 0,0022 m² eller mindre.
Stemmer det?
Med bare bilen på jekken påfører den et trykk på systemet på p = 14709.975 / 0,05 = 294,2 kPa. For at jeg skal oppnå det samme trykket må stempelet mitt være A = 637.432 / 294 200 = 0,0022 m². Jepp, det stemmer. Litt mindre så burde jeg ikke har noe problem med å løfte bilen.
Flyt og viskositet
Flyt i et hydraulisk system er bevegelsen av en mengde væske gjennom et punkt over en viss tid. Væsker er innelåst i slanger og rør i hydrauliske systemer, så flyt er væskens bevegelse gjennom disse.
Flyt (symbol Q) oppgis i liter per minutt (LPM) eller kubikkcentimeter per minutt (cm³/min) eller per sekund (cm³/sek).
Flyt = Areal (tverrsnitt) X Hastighet (Q = A x V)
Det er viktig når dette regnes ut å bruke korrekt enhet og verdi på begge sider av ligningen; dersom arealet oppgis i cm² og hastigheten i m/sek må det gjøres om til cm/sek og resultatet blir i cm³/sek, osv...
Viskositet er "tykkelsen" til en væske og i hydrauliske systemer er lav viskositet ønskelig. Jo lavere viskositet en væske har, jo mindre energi kreves for at den skal endre form eller posisjon. En økning i viskositet i en væske vil øke tiden væsken bruker på å bevege seg fra punkt A til B med det samme trykket. Altså vil flyten synke.
Utregning av viskositet er et kapittel for seg selv og ikke rent ukomplisert, men det måles hovedsaklig i Pascal-sekunder, som, hvis jeg skal slakte definisjonen av, betyr at med et trykk på 1 Pa beveger væsken seg X meter på ett sekund. Alle væsker har positiv viskositet, null viskositet observeres kun i supervæsker ved svært lave temperaturer. Generelt sett er væsker regnet som viskose dersom de er betydelig tregere enn vann.
Yoghurt har høyere viskositet enn vann. Hadde du brukt yoghurt i et vanngevær ville det ikke skutt særlig langt.
Flyten i et hydraulisk system beskrives enten som laminar flyt eller turbulent flyt. Vi liker å tro at væske beveger seg i den retningen man dytter den uten større problemer, men væske er stort sett turbulent. Laminar flyt er god flyt og er ønskelig, men vanskelig å oppnå.
Det hjelper å ha avrundede kanter i systemet og unngå skarpe ≥ 90 grader retningsendringer.
For å beskrive punktet når en væske eller gass går fra å være laminar til turbulent etter at den kommer ut av "kilden" brukes noe som kalles Reynolds-nummer (Re), introdusert av Sir George Stokes, og popularisert av Osborne Reynolds.
Bernoulli's prinsipp, oppkalt etter Daniel Bernoulli, sier at; når hastigheten til en væske øker, synker trykket proporsjonalt. Se video under for demonstrasjon av fenomenet. Det er verdt å nevne at det er ikke teknisk sett et mediums hastighet som fører til en trykkendring, men hastighetsendringen i seg selv som fører til trykkendringen.
Når en væske beveger seg gjennom et system vil den opprettholde lik flyt. Så dersom den går fra et stort rør til et mindre, vil arealet synke, så for å opprettholde samme flyten må naturligvis hastigheten til væsken øke. Dette kalles kontinuitet og beskrives med:
Arealet ganger hastigheten i punkt 1 er lik arealet ganger hastigheten i punkt 2.
Når dette skjer synker trykket. Når væsken går fra et lite rør tilbake til et større rør skjer det motsatte, at hastigheten vil synke og trykket stige.
Dette er også kjent som Venturi-effekten som er en utnyttelse av Bernoulli’s prinsipp.
Bernoullis formel ser normalt sett slik ut:
Formelen leses slik: Når flyten er konstant er trykket pluss massen ganger tyngdekraften ganger høyden over bakken pluss massen ganger hastigheten i annen delt på to lik i to ulike punkter i samme systemlinje.
Trykk i komprimerbare systemer
Pneumatikk oppfører seg litt annerledes enn hydraulikk, siden gasser er komprimerbare.
Boyle's lov, oppkalt etter Robert Boyle, sier at; ved konstant temperatur er forholdet mellom trykk og volum konstant i et lukket system med komprimerbar gass. Altså, når volumet synker, øker trykket. Eller rettere sagt, i en trykkluftkompressor, nårru stapper mer luft inn i samme tanken fårru større trøkk.
Forholdet i Boyle's lov uttrykkes med: P x V = k der P er trykket og V er volumet og k er konstant.
Matematisk kan den brukes slik:
Eksempel på Boyle's lov og atmosfærisk trykk. Flasken ble fylt med luft høyt oppe der det atmosfæriske trykket er lavt og når den ble fraktet ned komprimerte det utvendig trykket volumet på beholderen for å utligne trykket og inni og utenfor.
I praksis, skjematikk og symboler
I bruk kan et enkelt hydraulisk system se slik ut:
Hydraulisk olje
Reservoar
Filter
Pumpe
Flytretningskontroll
Hydraulisk sylinder med stempel
Linjer (rør eller slanger)
Overtrykksventil
Kjøler
Her representerer de rød linjene væske under trykk og de grønne representerer returlinjene.
Den hydrauliske sylinderen fungerer ved å kontrollere flytretningen til oljen slik at den blir presset inn foran eller bak stempelet slik at det blir produsert henholdsvis minusbevegelse og plussbevegelse, der stempelet går inn og ut respektivt. Pascal's prinsipper blir her observert ved den lille innløpsporten som er mye mindre enn overflaten til stempelet og mangedobler kraften.
Systemet over kan tegnes skjematisk slik:
De skjematiske symbolene for hydraulikk og pneumatikk ble utviklet av ANSI og adoptert av ISO.
Skjematiske tegninger viser koblinger, flyt, og funksjon til komponenter. De indikerer ikke fysisk konstruksjon av komponenter eller verdier og trykk, posisjon av kontroller eller koblingspunkter. Symboler tegnes vanligvis i nøytral eller normal posisjon.
Typen drift og retningen på flyten indikeres med en liten trekant slik:
Systemlinjer som er koblet sammen og linjer som bare krysser hverandre er indikert slik:
Begge måter er riktig.
Andre grunnleggende symboler:
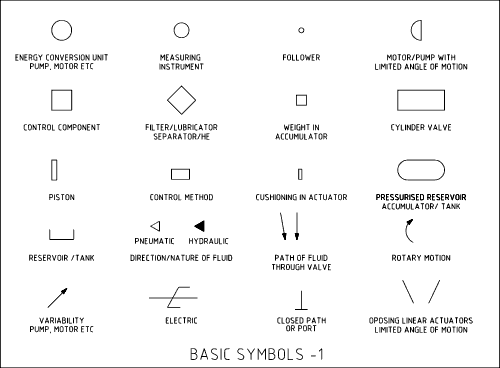
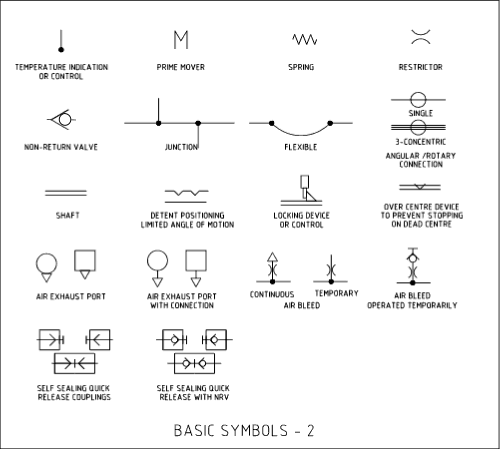
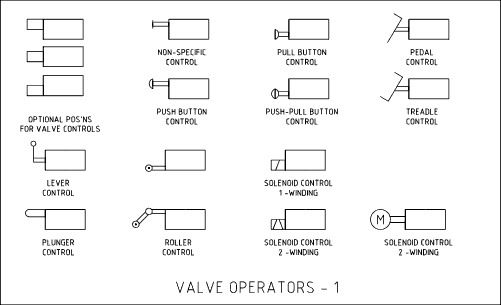
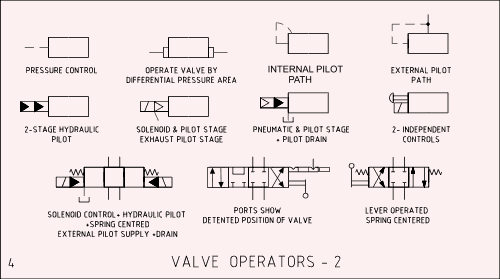
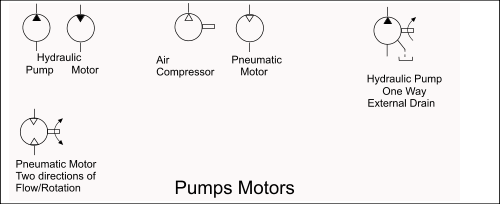

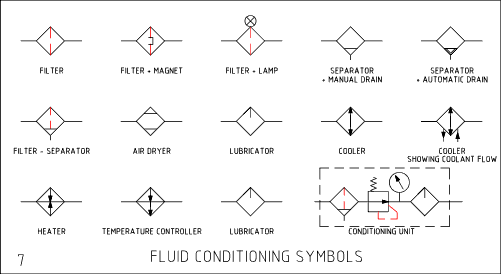
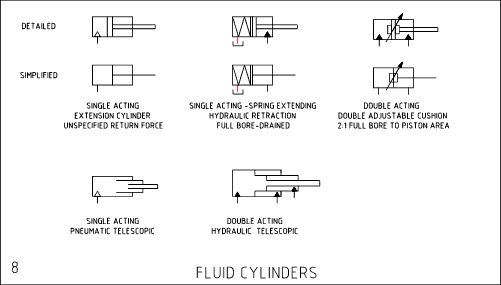
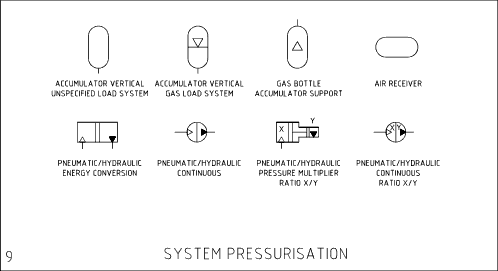